Новости компании
18 ноября 2014
80 лет технологической эволюции
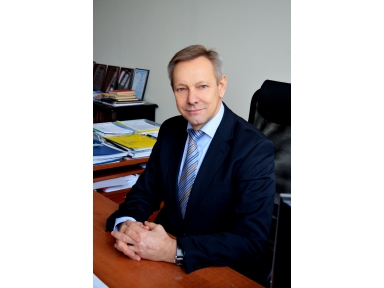
80 лет технологической эволюции
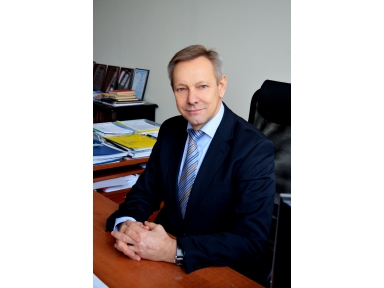
Рассказать об изменениях в технологии труболитейного производства на предприятии «Свободный сокол» за прошедшие 80 лет мы попросили директора по новым технологиям Александра Вилиевича Минченкова.
- Александр Вилиевич, какая технология производства труб использовалась на заводе «Свободный сокол» в 1934 году, когда был запущен первый труболитейный цех, и какие нововведения появились потом?
- В 1930-е годы использовался карусельный способ отливки труб – заливка производилась вертикально, в постоянную песчаную форму. Таким способом было возможно производство только труб из серого чугуна, толстостенных. Для обслуживания одной карусельной установки необходимо было порядка 20 человек. Производительность ее была невысокой, а процент брака, напротив, был достаточно велик. Используемые при таком методе песчаные формы быстро выходили из строя и не могли обеспечить точного диаметра раструба, поэтому возникали трудности при монтаже трубопроводов, и были частые прорывы в местах соединений. Эта технология была несовершенной, поэтому начались поиски новых способов производства чугунных труб. В 1954 году рассматривался вопрос о внедрении новой технологии центробежного литья. Конструкторский отдел завода «Свободный сокол» разработал чертежи центробежной машины, которая была изготовлена непосредственно на предприятии. На заводе был построен первый в стране цех по производству труб центробежным способом литья мощностью 230 тысяч тонн в год. В 1969 году после реконструкции труболитейного цеха была создана новая центробежная машина, которой было дано имя «Сокол». При этом для ее обслуживания было необходимо всего 5 человек, а ее производительность в сравнении со старыми карусельными установками, увеличилась в 2 раза, себестоимость продукции же ощутимо снизилась. Оборудование липецкого производства функционировало в труболитейных цехах № 1 и 2. В те годы сокольские чугунные трубы были очень востребованы: они использовались для строительства систем водоснабжения и мелиорации, которые активно создавались на всей территории бывшего СССР.
- На тот момент в производстве труб использовался серый чугун, каковы были его недостатки?
- Действительно, единственным материалом для производства труб был серый чугун, содержащий пластинчатую форму графита. А серый чугун – хрупкий металл. Главным недостатком тех труб и, соответственно, смонтированных из них трубопроводов была низкая прочность. При просадке грунта в осенний и весенний периоды происходили прорывы на трубопроводах. Их ремонтировали с помощью свинцовой начеканки непосредственно на место прорыва, или с помощью пакли, которую забивали в места разорванных соединений. В структуре городских водоканалов даже существовали специальные бригады, следившие за обнаружением и устранением неполадок в трубопроводах. К тому же труба не имела современных защитных покрытий, в целях предотвращения коррозии металла наносилось лишь покрытие из битума. Разумеется, подобный способ был далек от совершенства. И серый чугун как материал не позволял удовлетворять требования долговечной и безаварийной эксплуатации трубопроводов. Эта важная проблема обсуждалась тогда на уровне ЦК КПСС и Госплана СССР.
- Что позволило решить данную проблему?
- Еще в середине ХХ века был изобретен модифицированный чугун с включениями графита шаровидной формы, получивший название высокопрочного. Он значительно отличается от серого чугуна, обладает высокой коррозийной стойкостью, обеспечивающей долговечность эксплуатации и механические свойства стали – прочность на разрыв и пластичность. В Европе на тот момент уже существовало производство труб из высокопрочного чугуна с шаровидным графитом. В 1970-е годы было принято решение о внедрении в СССР технологии производства высокопрочного чугуна, а для изучения передового опыта во Францию была направлена группа специалистов. В июне 1972 года главный инженер завода А.П. Усачев в составе первой технической делегации посетил французскую фирму «Понт-а-Муссон», производящую трубы из ВЧШГ. В 1974 году в Минчермете были рассмотрены и утверждены предложения фирмы «Понт-а-Муссон» о ее участии в проектировании и поставке оборудования для строительства цеха по производству труб из ВЧШГ на заводе «Свободный сокол». А в 1980-м году был подписан контракт с фирмой «Понт-а-Муссон» на поставку оборудования для строительства нового цеха на «Свободном соколе». Помимо этого, в начале 1980-х годов на базе труболитейного цеха № 1 был организован собственный экспериментальный участок по разработке технологии получения высокопрочного чугуна с шаровидным графитом. Затем эти разработки были приостановлены. В конце 1980-х началось строительство нового цеха. Справедливости ради следует отметить, что тогда французы передали схемы устаревших соединений, уже не соответствовавших европейским стандартам, к тому же на линии производства труб не было установки оцинкования. Труболитейный цех № 1 А (ныне ТЛЦ № 3) был первым в СССР предприятием, выпускающим продукцию из ВЧШГ. Это было по-настоящему передовое производство: индукционные печи для плавки металла, модифицирование чугуна путем введения магния, гидротесты в целях контроля качества труб и тест на пластичность, линии по нанесению внутреннего цементно-песчаного и внешнего завершающего покрытия.
- Какими нововведениями ознаменовались 2000-е годы, когда труболитейное производство на «Свободном соколе» после кризиса 1990-х вновь стало расширяться и развиваться?
- Несмотря на то, что труболитейный цех № 3 был передовым для начала 1990-х производственным комплексом, в его работе, тем не менее, был ряд несовершенств. Так линия литья труб была французская (фирма «Понт-а-Муссон»), линия трубоотделки – немецкая (фирма «Будерус»), а часть оборудования, в частности стержневые машины, – советского производства. Естественно, возникали накладки в производственном процессе, были несовершенства в цикле изготовления трубы. Поэтому, когда в 2000 году начался новый подъем труболитейного производства на «Свободном соколе» возникла необходимость в ряде технологический усовершенствований и нововведений в соответствии с последними достижениями мировой практики. В 2004 году была установлена автоматизированная стержневая установка немецкой фирмы «Laempe», что позволило изготавливать стержни для производства труб европейского уровня качества. Был установлен индукционный канальный миксер американской фирмы «Inductotherm». С помощью представителей немецкой фирмы «Duker» была модернизирована гидравлика и электрика всех пяти центробежных машин. В 2005 году был проведен ремонт проходной печи отжига труб. Участок по производству труб стал по-настоящему высокотехнологичным, позволяющим изготавливать продукцию, соответствующую международному уровню качества. А в 2006 году начинается организация строительства линии по производству труб большого диаметра (Ду 350-1000 мм). Было несколько предложений по закупке оборудования. Выбор был сделан в пользу китайской фирмы «Wantong Industrial Equipment Co Ltd», которая изготавливает оборудование по немецким чертежам. Около месяца специалисты завода «Свободный сокол» провели в Китае: знакомились с процессом производства труб большого диаметра, вели приемку оборудования на поставку в Липецк.
- Какие разработки внедрялись в производственный процесс?
- Еще при строительстве нового трубцеха был приобретен патент на соединение RJ для производства труб, используемых при строительстве трубопроводов для поставки воды и природного газа. Долгое время велась активная работа над чертежами для производства соединения труб типа Tyton, которое было изобретено в США и является признанным в качестве международного стандарта. Сейчас мы производим продукцию с этим соединением. В 2003-м году сокольскими специалистами с учетом передового зарубежного опыта была создана установка оцинкования труб. В 2010-м году успешные испытания прошла наша собственная разработка – новый вид неразъемного соединения RJS для труб диаметром 400-1000 мм, которое незаменимо при строительстве водопроводных сетей в условиях гористой местности или просадочного грунта. Тогда же мы освоили производство труб с внутренним глиноземистым цементным и наружным цинк-алюминиевым покрытием, завершающим слоем эпоксидного покрытия-голубого для питьевой воды и красно-коричневого цвета, для канализационных систем.
- Какова на сегодняшний день технологическая стратегия труболитейного производства компании «Свободный сокол»?
- Производственный процесс требует постоянного поиска путей оптимизации и усовершенствования технологии. Иначе есть риск отстать от передовых тенденций и мировых стандартов. Поэтому идет непрерывный поиск новых видов добавок, способных улучшить качество чугуна, новых позволяющих сократить затраты на производство технологий, например для наплавки валика при изготовлении очень популярных труб с замковым соединением RJ и RJS. В частности сейчас идет строительство третьей установки по наплавке. Очень важная задача – это расшивки «узких мест» при производстве труб, а именно внедрение дублирующего оборудования линии трубоотделки, что позволит увеличить объемы производства продукции. Также это дальнейшая работа над усовершенствованием технологии нанесения цинкового и цинк-аллюминиевого покрытий, эпоксидного покрытия взамен лакокрасочного. Идет модернизация центробежных машин, а именно замена гидравлических приводов центробежных машин на более точные и экономичные электрические приводы. Также мы стараемся унифицировать процесс работы. Так на центробежной машине № 8 стало возможным изготовление труб Ду 600 мм, а в дальнейшем — труб Ду 500 мм. Это лишь часть из тех задач, над решением которых трудится и работники нашей дирекции по новым технологиям, и весь коллектив труболитейщиков.
- Александр Вилиевич, в чем, на Ваш взгляд, состоит уникальность труболитейного производства на «Свободном соколе»?
- Наш труболитейный цех – один из самых больших в Европе. Труболитейное дело на «Свободном соколе» является технологически передовым, соответствующим общепризнанным мировым стандартам качества выпускаемой продукции, единственным и уникальным для промышленного сектора России и стран СНГ производством. Здесь установлены мощные индукционные печи для плавки чугуна, есть крупнейший миксер, который способен обеспечивать бесперебойную подачу расплавленного металла при больших объемах производства труб. Также мы обладаем современным высокотехнологичным вспомогательным оборудованием, в частности стержневым комплексом «Laempe». Уникальность состоит еще и в том, что наша вся производственная линия предприятия соответствует самым передовым требованиям международных стандартов, предъявляемым к изготовлению трубной продукции из ВЧШГ. Мы обладаем уникальной технологией и оборудованием для нанесения внешних (цинкового и цинк-аллюминиевого) и внутренних (цементно-песчанного и глиноземистого) покрытий. Но главный актив предприятия – это высококвалифицированные и компетентные кадры, владеющие уникальной технологией производства трубной продукции из ВЧШГ, постоянно работающие над усовершенствованием выпускаемых труб и фасонных частей, вносящие успешно реализуемые предложения по оптимизации производственного процесса и уменьшения затрат на него.
Поделиться:
↑ наверх